INGEDE News October 2020 –
Special Edition
Autumn Symposium
- Calendar of Events
- INGEDE Autumn Symposium on October 1st at LEIPA in Schwedt
- Too much potentially recyclable paper in residual waste (Robin Huesmann, Leipa)
- “We want our material to go into the blue bin” (Bernd Büsing, Nestlé)
- “Perform our monitoring function more strongly” (Almut Reichart, UBA)
- High fibre quality has to be maintained in the cycle (Martin Drews, VDP)
- Assessment of recyclability: presentable method by November
(Samuel Schabel, PMV, and Tiemo Arndt, PTS) - How do you recycle, collect, compost, recover locally? (Peter Désilets, Pacoon)
- White packaging as a new paper grade? (Tobias Zirsch, REDWAVE)
- Paper from recovered paper – with organic waste and DVD dust (Sandro Taske, Leipa Schwedt)
- Links/in the media about packaging and recycling
- All presentations for download here
- SUBSCRIBE HERE to our newsletter!
INGEDE Autumn Symposium
on October 1st, 2020
at LEIPA in Schwedt
PACKAGING DESIGN
IN THE FIBRE CYCLE
Packaging protects. From contact, from dust, from moisture, from air, from damage. Modern packaging is multi-talented. Especially made of paper, especially in competition with plastic. But here, too, the following applies: Packaging is a reusable material that should be recycled in a high-quality way. The conflict of objectives is programmed – functionality and attractive design on the one hand and the best possible recyclability on the other. INGEDE wants to keep at least some of the white packaging remaining in the white fibre cycle.
How can packaging be optimally designed for high-quality recycling? Frozen pizza in a round tear-open pack made of paper, beer in a bottle made of fibre? Is this the future of packaging, fibre-based protection for food instead of plastic? At the INGEDE Autumn Symposium in Schwedt, experts from industry, authorities and associations discussed possibilities to replace plastic which has fallen out of favour, the prerequisites for good recyclability and its limits. The speakers were largely in agreement: There is a need for action with regard to the framework conditions, consumer information and labelling for new paper-based packaging, as well as for the further development of sorting systems and disposal routes. One had to move away from national towards European solutions in the evaluation of packaging and its suitability for different recycling systems.
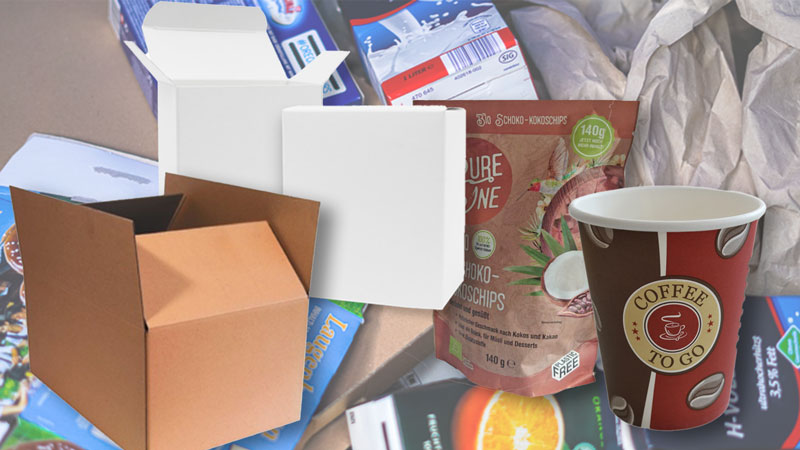
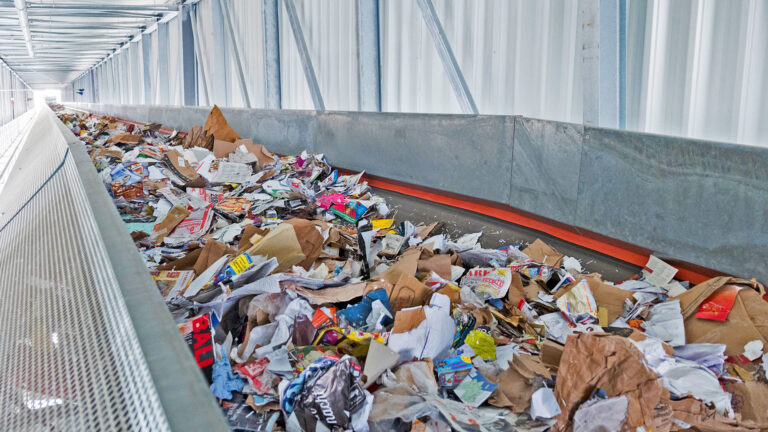
Too much potentially recyclable paper in residual waste
Paper, cardboard, and paperboard are the leading in Germany in terms of sustainability, with 89 percent of the material and more than ten percent of energy recovered based on a renewable raw material. However, too much potentially recyclable paper still ends up in packaging waste and residual waste, complained Robin Huesmann, CIO of the host LEIPA Group. In Schwedt, papers with the Blue Angel and other environmental labels are produced from 100 percent recovered paper. Huesmann noted a lack of consumer information, but also a lack of willingness to separate old newspapers, brochures, and boxes in the residual waste, even though the blue paper bin is right next to them.
Often uncertainty also plays a role: what do I do with the waxed wrapping paper, what about the water-repellent deep-freeze packaging? Is this paper for recycling? Huesmann is convinced that better information for consumers about both the products and packaging concerned and the available tonnes would also lead to better results in collection and sorting.
Different new composites require new types of recycling systems that are adapted to them, says Huesmann. More by-products in these processes may also require better solutions for the chemical recycling of these by-products.
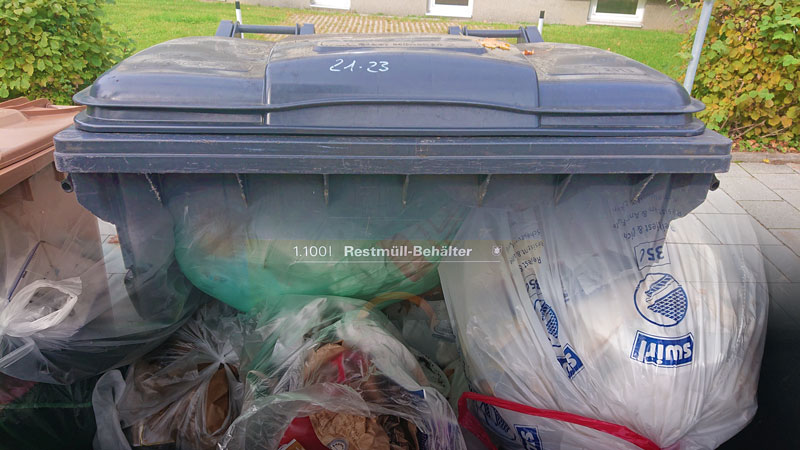
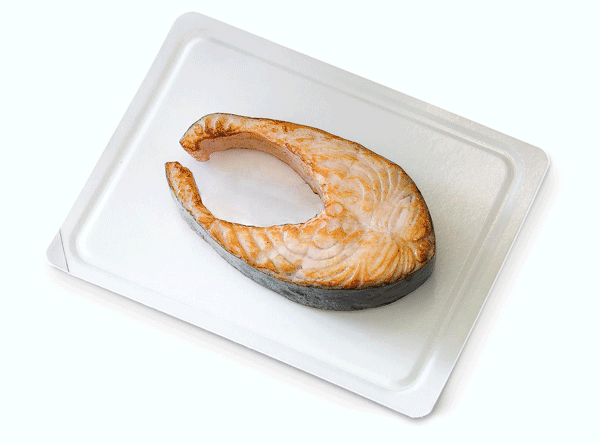
"We want our material to go into the blue bin"
Even if paper is currently in demand as a packaging material – it is not always enough as a barrier. “The devil is in the detail here,” says Bernd Büsing, head of packaging at Nestlé Germany. Nestlé has developed “high-barrier papers” for several products, which contain up to ten percent of a polymer dispersion as a coating. Is this a paper or a composite? Or a grey area? In Germany, in France? Büsing does not want to see such packaging being marked “plastic free”. But the goal is: “We want to go into the blue bin.” Therefore, he welcomed the intensified exchange between packers and the recycling paper industry, which was intensified by the INGEDE event.
By 2025, 100 percent of Nestlé’s packaging should be reusable or recyclable, by then the share of new plastic in packaging should be reduced by one third. This would also require changes in behaviour – and Nestlé intends to contribute to this by raising awareness of packaging. A number of products with low barrier requirements are already being packaged in functional papers. A cocoa bag, for example, consists of 80 to 90 percent cellulose, plus up to ten percent each of coatings made of pigment with latex and of a polymer dispersion.
"We have to monitor more strongly"
Ten percent polymers in paper are “not advantageous from our point of view”, confirmed Almut Reichart, environmental engineer and at the German Environment Agency (UBA) responsible for the pulp and paper industry. Avoiding packaging is always the authority’s top priority. She warned against an undifferentiated turning away from plastic: “Does paper still make sense when properties are required that paper cannot provide? Perhaps a plastic film would be the better material after all, if it was then disposed of or recycled properly? Reichart certainly sees a need for adaptation in the methods and standards for assessing recyclability. Not only manufacturers and associations, but also the authorities and in particular the Central Packaging Register must play a role here, said Reichart. “I can see that we have to perform our monitoring function more strongly here.”
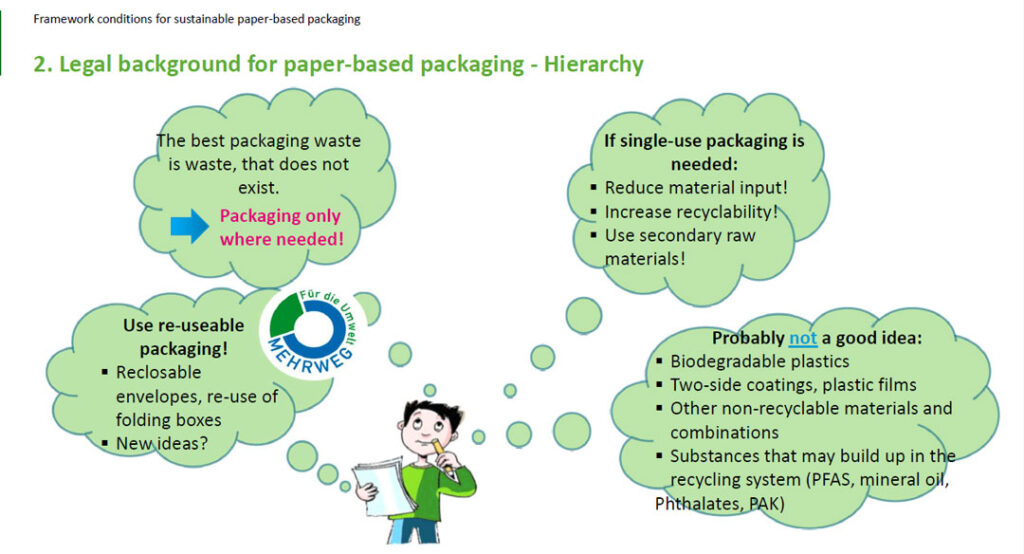
Avoid, reuse, recycle: Almut Reichart of the German Environment Agency (UBA) explains packaging hierarchy
High fibre quality has to be maintained
in the cycle
Martin Drews of the German Pulp and Paper Association (VDP) clarified the position of the paper industry: The blue bin has proven its worth and should not only be protected, but ideally implemented throughout Europe. Maintaining a high fibre quality in the cycle “must be our goal”. Not everything that is made of paper can be recycled industrially – it is important to consider which colour, which varnish, or which coatings are associated with it.
Adhesives must be easy to remove; “soft” adhesives such as some adhesive tapes and labels can hardly be removed during recycling. Ideally, barriers should also be easy to separate from the fibres, either mechanically or manually by the consumer. He also drew attention to the yellow bin: this must be the way forward for new types of packaging that cannot be recycled in the main stream of paper for recycling.
“Systematic differentiation in individual cases and a common understanding in the paper packaging value chain is the central challenge of the coming years.” Here, new recycling methods must also be considered. He warned against individual packaging manufacturers pushing ahead with new systems before their recycling has been clarified: “This creates confusion among consumers and hinders acceptance.”
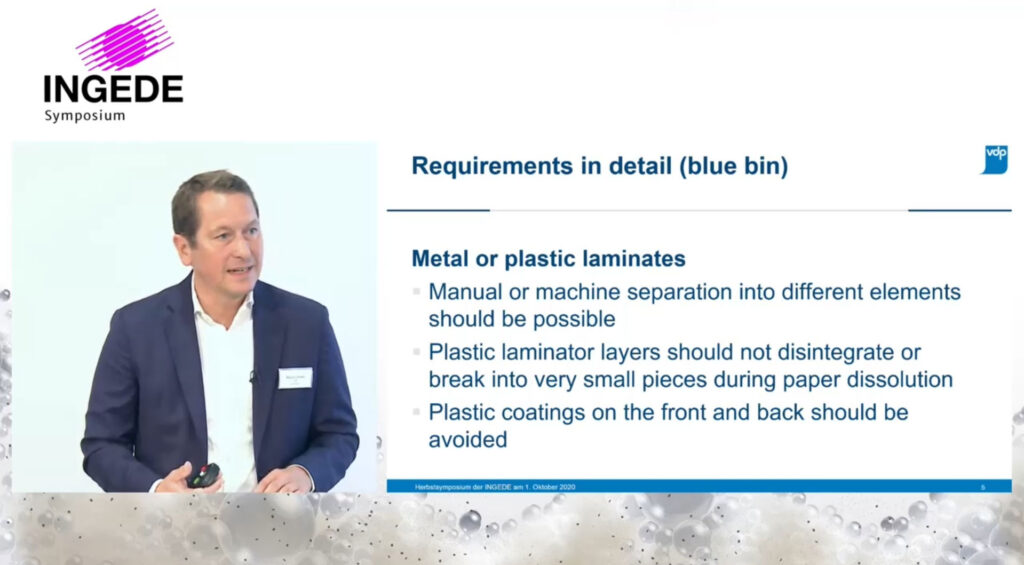
“Systematic differentiation in individual cases and a common understanding in the paper packaging value chain is the central challenge of the coming years.”
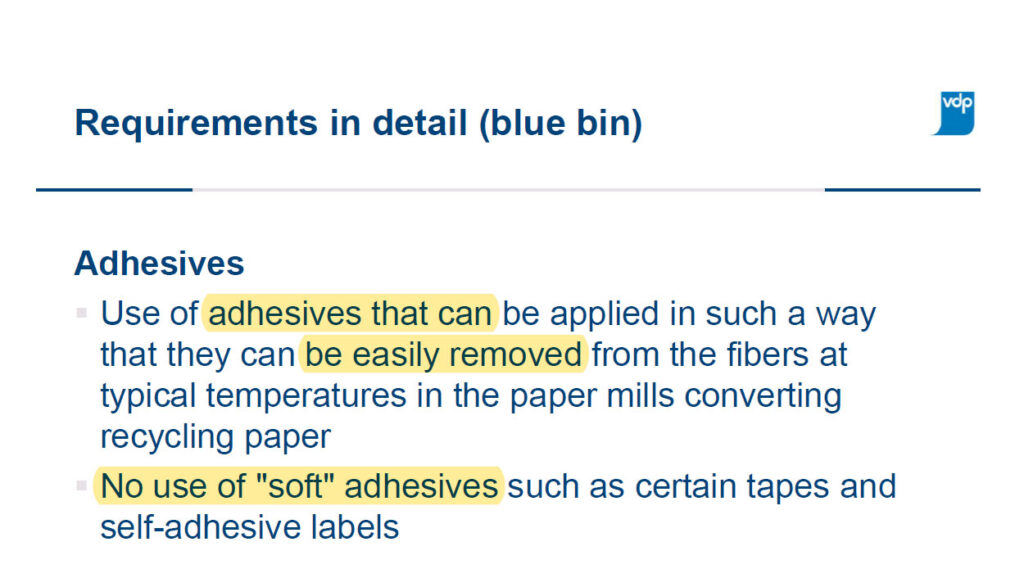
Assessment of recyclability:
presentable method by November
Prof. Samuel Schabel from the Institute for Paper Technology at TU Darmstadt also complained about the large number of new developments, where it is difficult to keep an overview. Together with other partners, including the Papiertechnische Stiftung (PTS), Darmstadt is looking for a uniform evaluation method for the recyclability of packaging.
“In the medium term, we will need a further technical step in reprocessing,” Schabel feared in view of the diversity of barrier materials. According to Tiemo Arndt of PTS, the INFOR-214 project aims to present “a presentable harmonised method” as a basis for discussion by November. He coordinates a CEPI project with the aim of distilling useful equipment and sample descriptions from the currently available descriptions from Aticelca to EcoPaperLoop to PTS.
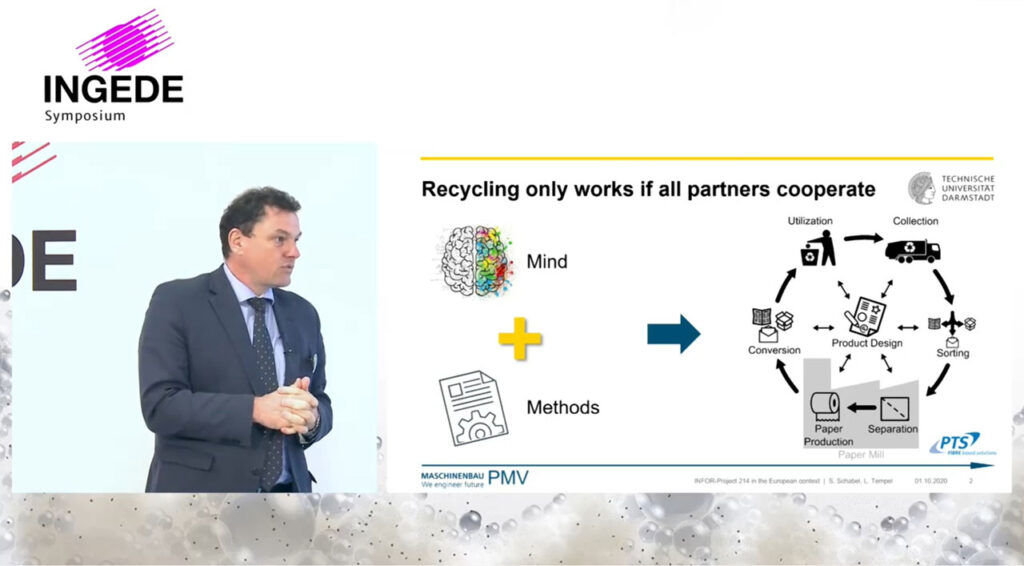
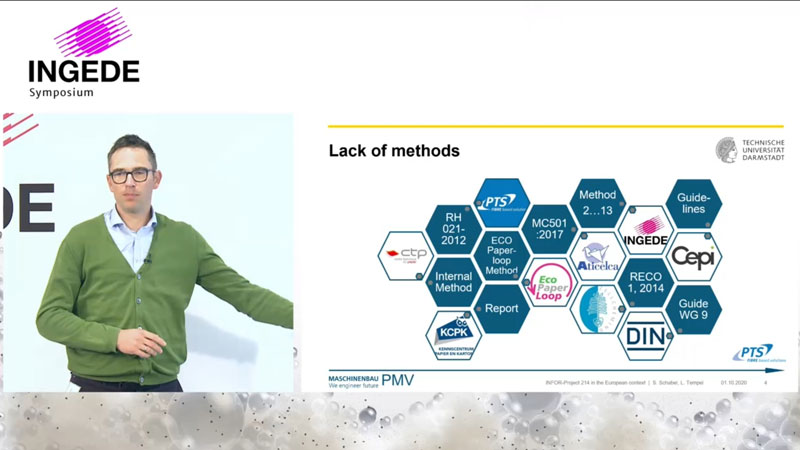
How do you recycle, collect, recover locally?
Peter Désilets of Pacoon also pointed out the current great differences in the collection of packaging in Europe. His Munich-based agency focuses on the development of sustainable packaging and packaging strategies. Depending on the market and region, it is necessary to consider whether and how packaging is actually recycled, collected, composted, or otherwise recovered locally. This is especially true in view of the current focus on carbon dioxide: “Would the fish or bird in the sea that swallowed plastic die with a better conscience if it knew that the plastic had a better CO2 value than a fibre pack that dissolved in water or decomposed on land?
The manufacturers of fibre packaging and the recyclers are also called upon to establish recycling standards at a higher level internationally. There are certainly possibilities to use intelligent combinations of plastic and fibres that can be easily separated again after use, as is already the case with some yoghurt cups.
Links/in the media about packaging and recycling:
Die große Verpackungslüge im Kühlregal
(WELT 3. September 2020)
How far can paper replace plastics?
(Packaging Europe September 21, 2020)
Unique formed fiber food service bowls to replace plastics
(Press release by Stora Enso Published 13 October 2020)
White packaging as new paper grade?
Is it possible to recover white fibres from light packaging collected from households or even from household waste? Is it possible to generate a separate grade of paper for recycling, “white packaging”? Tobias Zirsch from the sorting system manufacturer REDWAVE in Gleisdorf, Austria, addressed this question.
In a previously recorded contribution, Zirsch explained the possible construction of such a plant. It was important to know as much as possible about the composition of the fraction to be sorted from the very beginning. Sorting could also take place in several steps – first, the plastics would have to be separated, then generally fibre-based materials. Then – for example in a sorting plant – first the paper suitable for deinking and then the remaining white fibres could be separated from the rest of the packaging.
Paper from recovered paper – with organic waste and DVD dust? Every day a new challenge
Weapons, organic waste, potato sacks, and car tyres – there is practically nothing that has not already landed on the conveyor belts of the sorting plant. Apart from the problems with adhesives or printing inks that are difficult to deink, many things find their way into the paper bin that have no place there. Paper for recycling is a little different every day. Overall, the paper for recycling is getting darker and darker, Sandro Taske, head of the pulp division at Leipa in Schwedt, noted. As a result, the cost of chemicals, especially bleach, is also increasing.
The engineer is particularly concerned about the increase in digital prints with problematic deinkability. Here, the high-quality recyclability has to be taken into account already during the design of a print product. Foil-coated papers could also cause faults in the system. “Berlin is our forest,” says Taske, and at the same time lists all the waste this forest holds ready for paper recycling, from cobblestones to ammunition to medical waste. However, there are also black sheep among the disposal companies, who use their imagination to enrich the paper for recycling. Some bales drip even in fine weather, and dust from the DVD shredder or metal shavings from collective football pictures can have a lasting impact on the quality of the finished paper, and even lead to disruptions in the printing process.
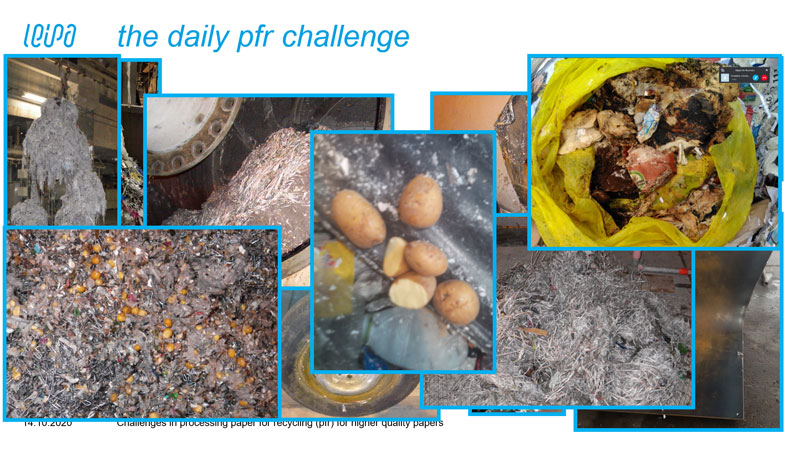
Sacks of potatoes in paper for recycling? That has just as little to do here as organic waste (above) or remains of DVDs and medical waste (below).
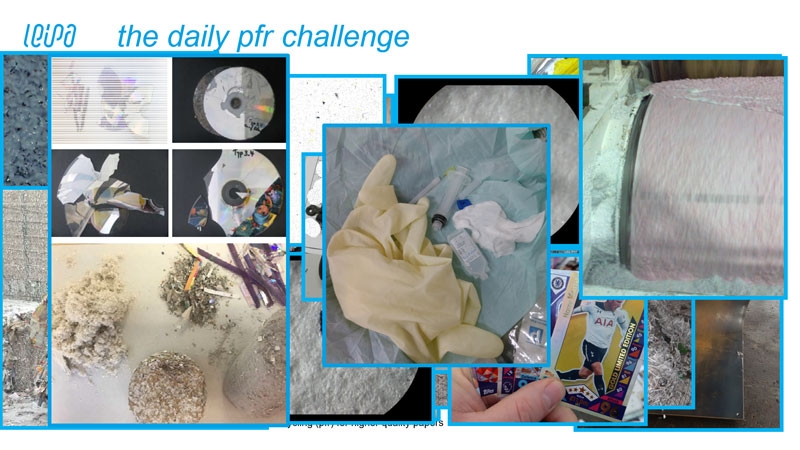
SUBSCRIBE HERE to our newsletter!